On the 845-kilometer route between Bühl in Baden and Szombathely on the Austrian-Hungarian border, the Schaeffler Group – one of the world’s largest automotive and industrial suppliers – uses 12 to 14 semi-trailers every day to supply the production site with transmission parts and drive components. 15,000 square meters is the production area of the Szombathely II plant, which is located three kilometers from the main plant opened in 1996. The new manufacturing facility is considered a center of excellence for e-mobility within the Schaeffler Group – and the first plant to operate on a climate-neutral basis throughout. In 2040, the Schaeffler Group aims to be 100 percent CO2 neutral, and production is to be climate neutral ten years earlier. Logistics also wants to make its contribution and set the course early on in the direction of emission-free or low-emission transport.
“Just in time doesn’t always have to be the case.”
Peter Egner, Head of Supply Chain Management and Logistics Automotive at the Schaeffler Group.
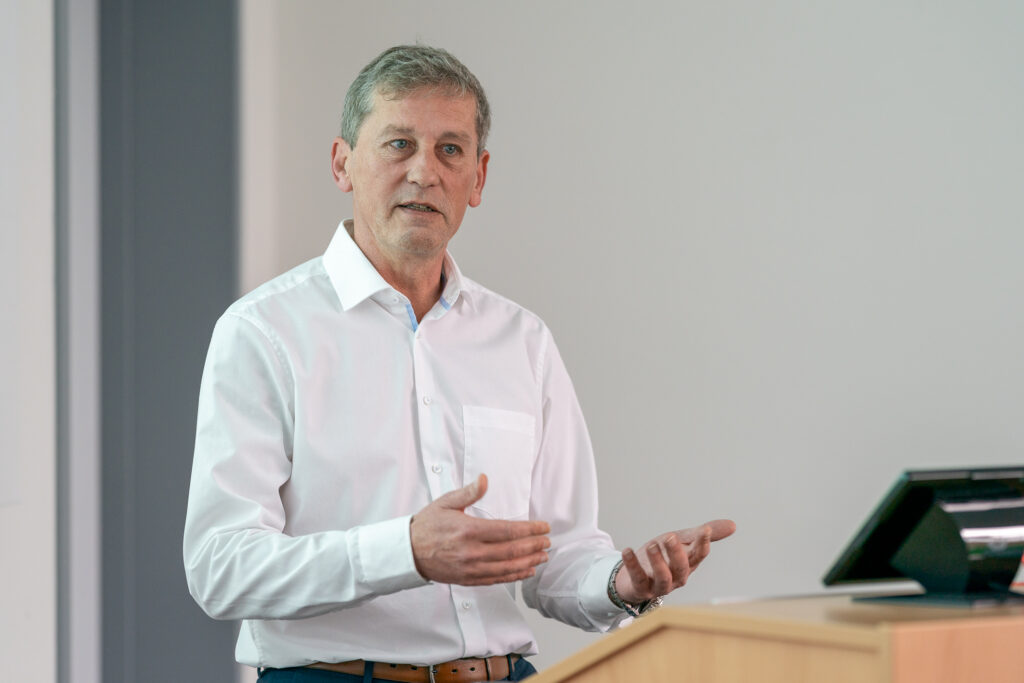
Road or road and rail combined
Peter Egner, Head of Supply Chain Management and Logistics Automotive at the Schaeffler Group, has therefore decided: We will conduct the intermodal test, pit two transport routes against each other, and then evaluate the results so that, if the findings are positive, we can increasingly focus logistics on rail. Thus, on February 18, two trucks loaded with the goods needed in Hungary set off from Bühl. A tractor-trailer combination from the Hungarian freight forwarder Domino Trans drove the entire route continuously on the road. A tractor unit from Logistik Schmitt in Bietigheim pulled a craneable Krone megatrailer from the plant premises in Bühl and proceeded on the highway to the combined transport terminal in Ludwigshafen, some 130 kilometers away. All under the eyes of the editors of the trade journal trans aktuell, who provided editorial support for the Intermodal test.
Rethinking logistics
With a cleverly combined mix of transport modes, the chances of actually achieving Schaeffler’s ambitious climate targets are good. For the automotive supplier, it therefore makes sense to shift the main leg of the journey from road to rail, especially on the heavily used transport corridor between Germany and Hungary. In order to save more air pollutants in transport, there must also be a general rethink in logistics, Peter Egner is convinced. “Just in time doesn’t always have to be the case,” he says, adding that intelligent and forward-planned transport runs can cushion volatile transport sequences. This is exactly what Schmitt Logistik has been working on, thinking through various approaches and discussing them with the Schaeffler logistics team. “The transports can be implemented in different ways, especially with regard to the equipment used. Depending on what is more important to the customer – be it price, availability or emission reduction – the individual logistics concept can look different,” says Managing Director Rainer Schmitt.
Ecoplus on rail with energy from wind and water power
80 percent of pollutant emissions from transport can already be saved today in terminal-to-terminal traffic between Ludwigshafen and the container terminal in Vienna. It is already foreseeable that in the short and medium term, traction service providers will use sustainable electricity to operate the modern electric locomotives. Because on the railroads, too, climate-neutral offers with energy from wind and water power are increasingly finding their way into the product portfolios of rail transport companies and intermodal operators. Pre-carriage and on-carriage are initially being carried out in pilot operation on the road using diesel power. In the opinion of those responsible at Logistik Schmitt, it is conceivable that this part could also be provided CO2-free by electric truck or with synthetically produced diesel in a later development stage. This would make transport completely climate-neutral using the truck and rail transport mode mix. Just as the Schaeffler Group envisions for its future logistics!
From Ludwigshafen via Wels to Vienna
The intermodal connection used for the pilot service starts in Ludwigshafen and runs via Wels to Vienna. Three times a week and in A/C running time. At the gateway hub in Wels, semi-trailers, swap bodies and containers simply transfer to the train to Vienna, just as people do in passenger transport. In the case of Schaeffler, Marijo Pesic, Head of Eastern and Southeastern European Transport at Kombiverkehr, recommended that the on-carriage be made from the Austrian side to Szombathely in Hungary, even though direct services exist to Budapest. However, the pre- and on-carriage from the Hungarian capital would be “against freight.”
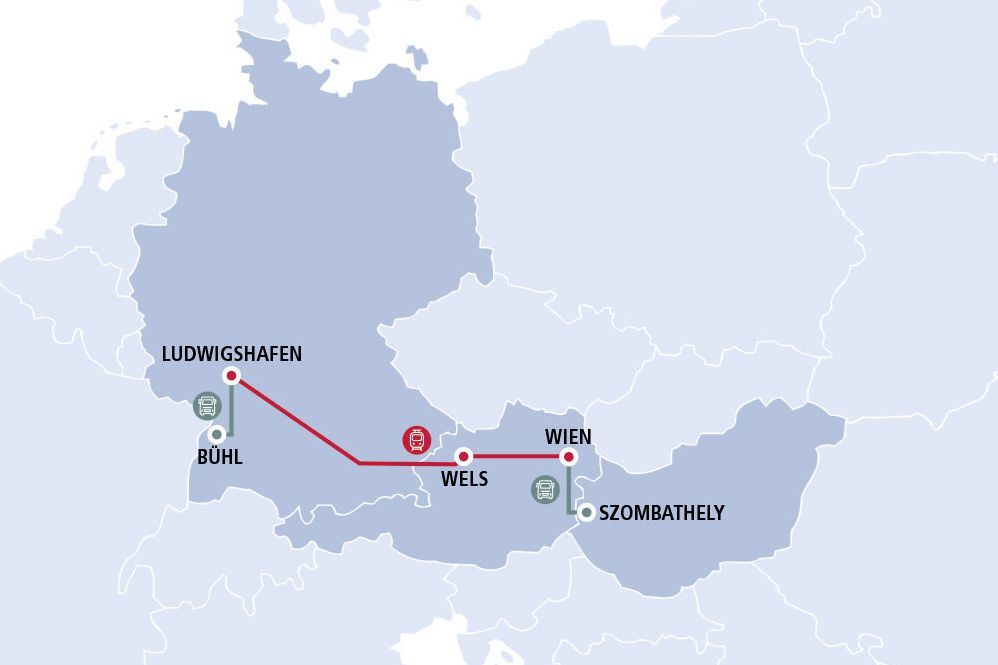
Kombiverkehr sales manager Peter Dannewitz outlined his expectations for the pilot transport as follows: “That we succeed in convincing with our performance and demonstrate a particularly sustainable alternative to road.” Apart from the better environmental balance, intermodal transport scores additional points: forwarders are allowed to carry four tons more, are exempt from vehicle tax, can also transport by rail on Sundays and public holidays, require fewer personnel and reduce their vehicle costs. “In addition, intermodal transport offers SMEs great growth potential while minimizing risk,” Peter Dannewitz particularly emphasizes.
Exactly on schedule, the Kombiverkehr train set off for Wels that evening, with the rail transport company Lokomotion as tractionary. 30 to 40 lattice boxes with total weights of 21 to 22 tons are on board the two trailers, which are moved once by Logistik Schmitt in intermodal transport and by Domino Trans in pure road transport.
Safety, availability and stability are the decisive factors
Intermodal or road transport: Which of the two transport modes has now won the race? At least three aspects play a role: transit time, costs and environmental protection. Intermodal transport doesn’t have to hide on any of these points – on the last one, it’s clearly ahead. “We will probably never completely get away from trucks,” says Egner’s colleague Karsten Erfmann, Head of Supply Chain Management at Schaeffler’s Bühl site. And Peter Egner adds, “The train is an excellent addition for us.” He is aware that the CT connection cannot cost exactly the same to the penny as pure road transport. “On the other hand, I can’t pay many times the freight for rail either.” And for Peter Egner, transit time is also only one of the factors in the evaluation. “Safety, availability and stability are just as decisive for us.” All the more reason why he is now looking forward to an in-depth and critical analysis of the test run.
Schaeffler’s logistics in figures
53 plants worldwide
29 warehouses
3,600 logistics employees
18,400 articles
750,000 part numbers in the system
3,000 suppliers worldwide
680,000 tons of steel required per year
632 regular connections between plants
Comments are closed.